Projects
1-Development of multiscale computation methodologies
Mechanical waves Harvesting devices are currently designed mainly using mass-spring models subject to harmonic excitation. VEH is however inherently time dependent, additionally we are targeting the optimisation of meta-harvesters and their integration in complex sources, and so a more realistic approach is required: We will adopt a multiscale approach based on substructuring the problems into large- and small-scales. The large-scale will use finite, or spectral, element time domain simulations to compute a database of realistic 3D wavefields for each of the target applications including: groundborne vibration propagation in realistic soils, structural vibrations on bridges, high rise structures, airplanes and train frames. The simulated wavefield at the desired location is then to be used as the input to small-scale detailed modelling of the harvesting device. The aim here is to reproduce, with high fidelity, both the metasurface dynamics and the coupling with the piezoelectric transducers embedded in the resonators of the metasurface. The meta-harvester design (type of resonators, and size, materials etc) will be specifically tailored to the frequency band and the polarisation of the input signal. Whenever necessary, modelling will include non-linear phenomena (e.g. bistable resonators, contact phenomena) and damping.
Interface circuits To enable harvesting from multiple piezoelectric transducers (each optimised for a different frequency band), diode-less rectifiers must be implemented. The advantage is that the circuit model can be lumped into a system of ordinary differential equations (ODEs) dependent on the property of the piezoelectric material and the electric load, and is then easily coupled to the mechanical model of the meta-harvester. These ODEs will be solved at run-time as lumped parameter systems using Runge-Kutta integrators.
Multiphysics models Depending on the problem scale, and design stage, the optimal software will be used and this requires drawing on the know-how and expertise of the partners across multiple software. 2D/3D elastodynamic simulations will be computed using state-of-the-art spectral and finite element solvers both in time and frequency domain.
2-Meta-harvester design optimisation for different applications
Metamaterial enhanced energy harvesting. (a) Examples of different resonators that can be used for different wave polarisations or for different type of vibration guiding. (b) One of the candidate designs that will be explored in the proposal for enhanced energy harvesting and non-linear frequency-up conversion. (c) Different scales and fabrication techniques for the meta-harvesters.
Metamaterial design The metasurface is at the heart of the harvester design and its optimisation is essential. The current state of the art, as shown in the figure above, relies on a cluster of linear graded resonators. A number of design enhancements of incremental complexity will be introduced. Improved focusing performance will come from the adoption of exponential grading profiles and their optimisation. At a later stage we plan to introduce topological metasurfaces to exploit topologically protected edge states to halt waves inside the harvester-resonator and prevent the back scattering occurring in non-topological designs; one of the partners (ICL) has substantial expertise with resonant topological metasurfaces.
While the proof-of-concept design made of rods on a plate is ideal for flexural waves in thin plates, it is limited in scope and multiple extensions are required: harvesting with other types of resonators and polarizations, deep substrates and anisotropic materials. Auxetic and mode separation designs allowing for a better dynamic range and coupling with multiple polarization will also be incorporated. Designs will be adapted to the lengthscale specifically required by each application, from the microscale to the centimetre or metre scale.
Coupling, and transmission, of vibration into the meta-harvester: A critical aspect, and one upon which we will focus, is that of the coupling between the host structure and the harvester, and in particular we aim to maximise the vibration fed into the metasurface; with this in mind we will integrate non-linear frequency up converters with the meta-harvester. Two strategies will be pursued: The first will enclose one or more frequency-up converters into a metasurface with linear behaviour as this will give the possibility of maximising the metasurface performance, and hence the harvester, regardless of the frequency band. The second strategy will directly integrate non-linearities in the metasurface’s resonators. Whilst this is much more complex and ambitious, this second option could deliver breakthrough improvements to the meta-harvester. It is currently unknown which of these two strategies will perform better and also satisfy manufacturing and cost constraints. The optimal solution will be dependent upon studies vis-a-vis the frequency band and the metasurface size and on the frequency; we aim to achieve VEH from very low frequencies, down to 1 Hz for instance.
Application type and size: Substantial differences exist, for instance, between harvesters installed on a fixed structure (building, bridge, dams), on the ground surface or directly embedded in a smart-frame. Equally substantial, are the differences between MEMS harvesters (microscale) aimed at powering ultra low energy sensors (pW) and portable, but yet centimetre or metre, large harvesters aimed at producing higher powers (mW). In this project both scales will be considered.
Design optimisation will be addressed within different application families: (1) geophysical applications and continuous structural health monitoring (SHM) to be installed on the Earth's surface or structures. (2) Sensors permanently embedded in smart-structures, (3) Sensors requiring only occasionally very low power and of very small size (e.g. wearable devices).
3-Meta-harvester fabrication
A high level of design integration can be achieved by exploiting additive manufacturing for the different fabrication steps of the meta-harvester. We will first fabricate the metasurface, and then add the piezoelectric transducers with this approach used for centimetre scale models as well as for those at the microscale. For metre-scale harvesters, their fabrication will rely on conventional machining and workshop tooling.Interface circuits
Metasurface fabrication Harvesting is best achieved using low-damping materials such as metals and alloys. The metasurface, whose task is to guide and focus the elastic energy in the harvester, is usually complex to manufacture, in particular if it has a 3D design and limited dimensions. Depending on the scale, different techniques will be used. Additive manufacturing of metals is ideally suited for meta-harvesters made of centimetre size resonators; the specific geometry of the resonators (free standing, and suspended element) makes Selective Laser Sintering and Melting (SLS and SLM) the most suitable techniques as they do not require support material (which makes fabrication problematic, especially when numerous resonators need to be printed at the same time).
Lead-free piezoelectric MEMS harvesters are typically represented by a thin cantilever with a tip mass and these are realized by standard micromachining processes for epitaxial Silicon, e.g. deep reactive ion etching (DRIE). The piezoelectric layer is typically deposited on the Silicon layer by means of Sol-Gel process (for PZT) or via sputtering (for Lead-free materials such as AlN and KNN). Apart from these industrial processes, in the present project we plan to make extensive use of rapid prototyping procedures based on 3D printing. Among the possible techniques it is worth mentioning that a new F-Serie printer from Ceradrop has been recently installed in POLIMI, in the framework of the Joint Research Center with STmicroelectronics. The machine combines conventional ink-jet printing with aerosol-jet technology, largely extending the range of possible materials deposited with a printing resolution down to 10 $\mu$m. Multiple heads can be used to print up to five different inks at once. Post-processing modules like vacuum drying, near-infrared and ultraviolet curing are available in line. Provided a suitable piezoelectric ink is achieved, the machine allows for the development of innovative processes for MEMS fabrication.
Microscale fabrication and testing ST Microelectronics has an essential role in the project as they bring unique know-how and facilities to the consortium with regards to the fabrication, and integration, of metasurfaces in MEMS harvesters. Using micromachining, a technique encompassing multiple steps of photolithography, wet and dry etching and micro-assembly on a silicon wafer, very complex shapes can be obtained, including those required by metamaterials. While technically possible, to date very few meta-microstructures have been fabricated and their integration with piezoelectric transducers is non-trivial
Interface circuits A key component of any harvesting system is the energy management and transfer interface with the final device; high efficiency is essential to avoid wasteful dissipation. The operating condition currently considered, for most energy management architectures in vibration energy harvesting, is the simple sinusoidal regime that comes from assuming single-frequency input vibrations: We will extend the concept of impedance matching for optimal energy extraction towards multi-frequency or broadband adaptation.
4-Laboratory and field validation
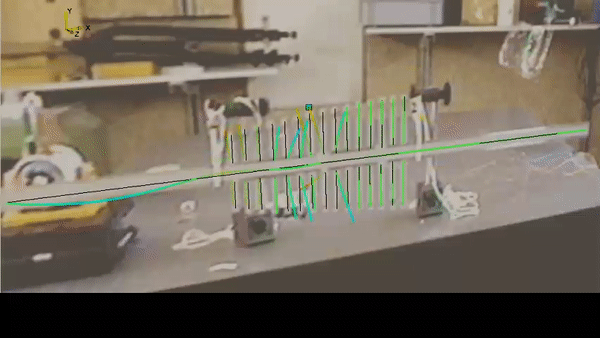
Laboratory experiments on the harvester prototypes will exploit cutting edge equipment such as our Polytech 3D laser Doppler vibrometer (3D LDV) mounted on a robotic arm, 3-axis piezoelectric actuators by Physikinstrumente, electrodynamic shakers and dedicated multichannel electronics to conduct experiments in a fully automated way. In both the ETHZ and POLIMI laboratories, real scale structures are available to test the coupling of the harvester with host; in ETHZ a large number of components from structures (e.g. bridge piles and girds, columns and frames) are available for dynamic testing. The laboratory also features: a large sandbox substrate mimiking the Earth surface that uses microm- eter glass beads (sand-like granular material) to mimic slow travelling surface waves at reduced scale (vs=50-100 m/s at 400 Hz, wavelength ∼ 20 cm) [45] and a set-up to generate and study wind-induced vibrations. POLIMI has long-standing experience with the dynamic testing of car and train frames where harvesters and sensors can be embedded: this is an ideal set-up for smart structure wireless sensors. The availability of these unique facilities and equipment allow us to benchmark and optimise the harvester performance in the actual working conditions across the 1 to 100 Hz frequency band. Low-power sensors necessary for complete tests will be provided by ST. Continuous feedback between experiments and simulations will allow us to (1) isolate possible non-linearities or unexpected behaviours (2) calibrate numerical models, (3) carry out proper uncertainty quantification over design parameters and performances.
Field experiments will focus on demonstrating the capacity of the developed harvester to work in actual applications and to test low power data transmission solution (see point v). Project partners at ETHZ have extensive experience in structural health monitoring (SHM) monitoring on bridges, wind turbines and rail track. At least one field experiment will be carried out during the project. A meta-harvester for instance will feed a low-power MEMS accelerometer provided by ST installed on a structure for several weeks. The self-powered sensors will be paired to a traditional one to monitor possible power shortages and their cause. This experiment will also allow us to validate the effect of temperature and humidity on the power production; this is a very important aspect since many sensors will be regularly exposed to atmospheric agents.
5-Data transmission and management
Laboratory experiments on the harvester prototypes will exploit cutting edge equipment such as our Polytech 3D laser Doppler vibrometer (3D LDV) mounted on a robotic arm, 3-axis piezoelectric actuators by Physikinstrumente, electrodynamic shakers and dedicated multichannel electronics to conduct experiments in a fully automated way. In both the ETHZ and POLIMI laboratories, real scale structures are available to test the coupling of the harvester with host; in ETHZ a large number of components from structures (e.g. bridge piles and girds, columns and frames) are available for dynamic testing. The laboratory also features: a large sandbox substrate mimiking the Earth surface that uses microm- eter glass beads (sand-like granular material) to mimic slow travelling surface waves at reduced scale (vs=50-100 m/s at 400 Hz, wavelength ∼ 20 cm) [45] and a set-up to generate and study wind-induced vibrations. POLIMI has long-standing experience with the dynamic testing of car and train frames where harvesters and sensors can be embedded: this is an ideal set-up for smart structure wireless sensors. The availability of these unique facilities and equipment allow us to benchmark and optimise the harvester performance in the actual working conditions across the 1 to 100 Hz frequency band. Low-power sensors necessary for complete tests will be provided by ST. Continuous feedback between experiments and simulations will allow us to (1) isolate possible non-linearities or unexpected behaviours (2) calibrate numerical models, (3) carry out proper uncertainty quantification over design parameters and performances.
Field experiments will focus on demonstrating the capacity of the developed harvester to work in actual applications and to test low power data transmission solution (see point v). Project partners at ETHZ have extensive experience in structural health monitoring (SHM) monitoring on bridges, wind turbines and rail track. At least one field experiment will be carried out during the project. A meta-harvester for instance will feed a low-power MEMS accelerometer provided by ST installed on a structure for several weeks. The self-powered sensors will be paired to a traditional one to monitor possible power shortages and their cause. This experiment will also allow us to validate the effect of temperature and humidity on the power production; this is a very important aspect since many sensors will be regularly exposed to atmospheric agents.